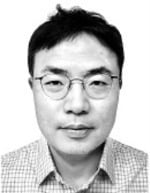
KAIST는 현실을 모사한 디지털 트윈기술을 활용해 한 달 이상 걸린 신제품 설계 및 생산기획 프로세스를 단 한 시간으로 줄일 수 있는 가능성을 제시했다. 그 가능성의 핵심은 전통적인 설계-기획-보고 체계의 디지털 전환과 프로세스 혁신이다.
타이어업체는 고객인 차량 제조업체로부터 개발될 차량의 기본적인 콘셉트와 요구사항을 전달받고, 이를 기반으로 신차에 맞는 타이어 설계 및 생산 비용을 산출해 고객에게 견적을 제시한다. 예를 들어 현대자동차에서 새로 개발하는 차량의 콘셉트와 엔지니어링 요구사항 그리고 생산 물량을 받으면 여기에 맞는 타이어 기초를 설계하고 생산에 필요한 생산 투자비 등을 산출해 견적을 제시한다. 이런 작업을 반복해 고객에게 맞는 타이어 및 생산 단가를 최종 결정한다.
이와 같은 신제품 설계-생산 기획 프로세스는 외관 디자인팀, 엔지니어링 설계팀, 연구소, 생산기획팀 등 다양한 부서의 협업이 필요하다. KAIST는 타이어 외관 디자인과 소재 선택에서 인공지능(AI) 기술을 통해 고도화할 수 있는 가능성을 검증했다. 특히 타이어의 외관 패턴 디자인은 최근 급속한 발전을 이루고 있는 ‘생성적 인공지능’이란 방식을 통해 과거 디자인된 패턴을 파악, 인공지능이 새로운 디자인을 창조할 수 있다는 결론을 내렸다. 그리고 소재 디자인에서도 디지털 트윈 기술의 핵심인 가상 시뮬레이션을 활용해 고객 사양에 맞는 최적의 물성 조합을 고르는 방식도 개발했다. 대량생산을 위한 장비 추가 도입 및 비용 산출도 수학적 최적화 알고리즘을 통해 단 몇 분에 산출할 수 있음을 도출했다.
즉 디자인팀, 엔지니어링 설계팀, 연구소, 생산기획별로 인공지능 기술, 시뮬레이션 기술, 최적화 알고리즘을 통해 부서별 의사결정이 자동화 및 고도화가 가능하다는 결론을 내렸다. 하지만 기존 1개월 이상 걸리는 작업을 단 몇 시간 만에 가능하게 하려면 부서별로 쪼개진 업무를 각각 자동화하는 것만으로는 부족하다. 의사결정이 지연되는 이유는 그 자체 시간이 걸리기보다 업무 대기시간이 늘어나기 때문이다. 이는 우리가 놀이공원에서 놀이기구를 타기 위한 대기시간이 긴 것과 마찬가지다. 또 다른 이유는 어려운 판단일수록 그 판단을 유보하는 사람의 본성 때문이다. 특히 경험 부족에 의한 자신감 결여로 판단을 미룰 수 있다.
KAIST는 문제 해결을 위해 두 가지 방안을 제시했다. 첫째 디자인, 엔지니어링 설계, 생산 기획의 모든 과정에서 사람의 의사결정을 배제한 전 과정 자동화를 제시했다. 그리고 이 과정에서 디지털 트윈 개념 도입을 제안했다. 실제 업무를 모사한 디지털 환경을 구축, 다양한 가상 시뮬레이션을 통해 가상 공간에서 다양한 경험을 하면서 최선의 판단을 자동으로 내리는 것이다.
기존 부서별로 나눠진 작업을 디지털 트윈 환경에서 데이터를 통합하고 일련의 프로세스를 가상화한 뒤 앞에 설명한 프로세스별 인공지능과 최적화 기술을 함께 구축해 최적의 의사결정을 자동화하는 기술이다. 물론 사람의 의사결정을 완전히 배제하는 건 아니다. 최종 디자인이나 비용이 도출되면 마지막에는 사람이 개입해 이를 보정한다.
이런 디지털 트윈 환경을 통해 한 달 넘게 소요되는 디자인, 엔지니어링 설계, 생산 기획 작업이 단 한 시간 만에 가능한 것을 입증했다. KAIST와 타이어업체의 이런 협업은 현재 진행형이다. 시스템 구축을 위해서는 단순히 기술 도입뿐만 아니라 부서 간 데이터 통합, 부서 간 성과지표 개선 그리고 조직 의사결정 체계 개선도 필요하다.
디지털 혁신이란 단순한 기술 적용만이 아니다. 기술을 기반으로 조직의 프로세스 변화와 전사적인 조직 변화를 필요로 한다. 결국 기술을 이해하고 조직의 변화를 주도할 수 있는 리더의 능력과 결단이 요구된다.
관련뉴스