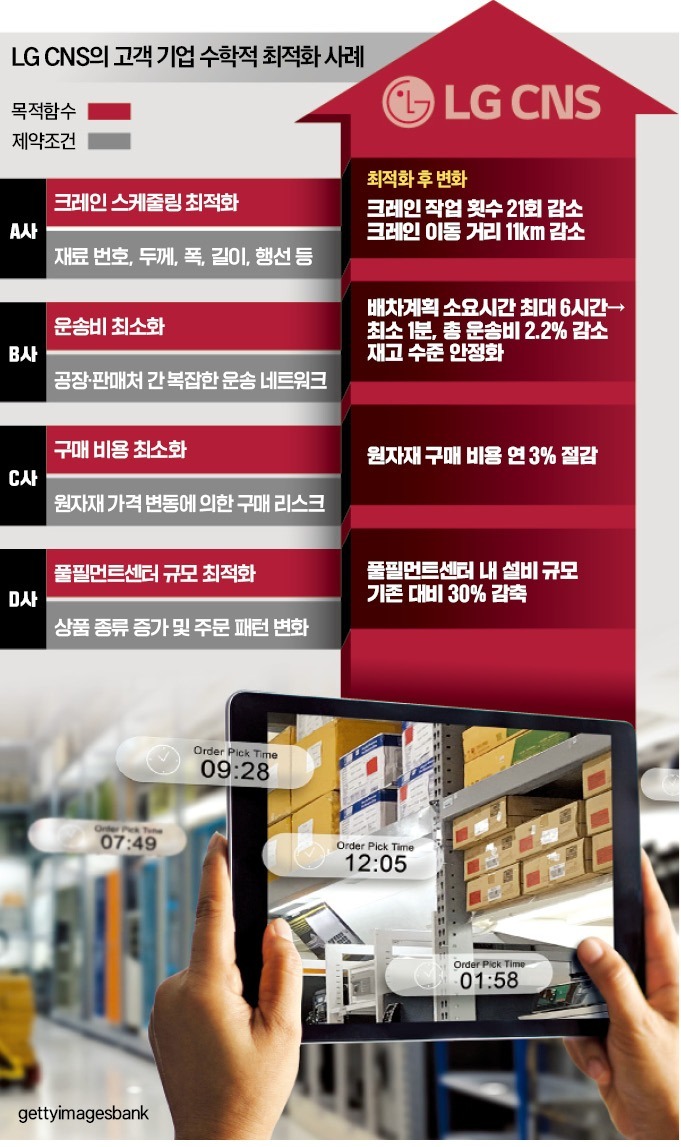
21일 업계에 따르면 LG CNS는 2014년부터 고객의 모든 상황을 숫자로 정리해 데이터화했고 이를 바탕으로 ‘커스터마이징 솔루션’을 제공하며 100개 이상 프로젝트를 진행했다. 대표 사례로는 슬라브(철강 반제품) 입출고 스케줄 변동으로 어려움을 겪던 철강 회사 A사가 꼽힌다. A사는 야드(yard·적재 공간) 효율성을 끌어올리기 위해 슬라브 적재·크레인 스케줄 최적화를 꾀했지만 진척이 더뎠다. 지시 사항이 400개 이상인 데다 수작업이 85.3%에 이를 정도로 자동화율이 저조했다. LG CNS는 재료 번호, 두께, 폭, 길이, 행선 등 슬라브 정보, 야드 적재 상황, 크레인과 입출고 정보 등을 기반으로 최적화했다. 출고 계획과 적재 위치, 크레인 작업 순서를 자동화하는 최적화 엔진을 개발한 결과 동일 작업량 기준 크레인 작업 횟수는 1261회에서 1240회, 크레인 이동 거리는 8만9149m에서 7만8023m로 줄었다.
제조 기업 B사는 복잡한 운송 계획 때문에 골머리를 앓았다. 사람이 엑셀로 계획을 짜다 보니 비효율이 발생했다. 갈수록 배차 계획이 꼬이면서 재고 보관량 증가로 비용이 상승했지만 운송사 계약, 거리 등 복잡한 배차 조건 때문에 비용 절감은 엄두도 못 냈다. LG CNS는 차량별 동일 화물 운송을 위한 화물 재정렬을 적용했고, 운송비와 연계 비용이 최소화되도록 할인이 가능한 편도 운송을 수학적으로 조합했다. 배차 계획 수립 소요 시간이 4~6시간에서 1~10분으로 단축되고, 재고 수준 안정화는 1.6%에서 69%로 개선됐다. 총운송비도 2.2% 절감됐다.
자재 구매에서도 성과가 상당하다. 배터리 제조사 C사는 원자재 구매비, 운송비, 금융비, 창고비 등 복잡한 비용함수와 원자재 가격 변동에 따른 구매 리스크가 갈수록 커져 가격 대응에 어려움을 겪었다. 생산 계획 수립과 다양한 시나리오 분석을 빠르게 할 수 있는 통합 툴의 필요성을 느낀 C사는 LG CNS와 손잡고 양극재 구매 비용 최적화 엔진을 개발했다. 자재 수요와 재고량, 원자재 가격(예측치), 물류 네트워크 등 데이터를 바탕으로 비용 최소화라는 목적함수를 설정했다. 조달, 공급, 창고 운영, 운송 수단 등 제약 조건과 양극재 구매량 및 시점을 결정 변수로 책정해 솔루션을 도출했다. 이를 통해 기존 대비 자재 구매 비용을 연간 약 3% 절감했다.
유통 기업 D사는 물류센터 자동화 설비 운영 계획을 짜는 데 수학을 접목했다. D사는 온라인 주문당 상품 수 등 주문 패턴이 들쭉날쭉하고 상품 종류가 급증하는 등 복잡도가 갈수록 높아져 고민이 많았다. 이에 따라 풀필먼트센터의 적절한 규모를 예측하는 것도 과제였다. LG CNS는 제품 보충 순서와 주문 처리 순서를 데이터로 설비 운영 최적화 알고리즘을 개발해 D사의 새로운 물류센터에 적용했다. 그 결과 기존 방식보다 설비를 30% 감축하고 저장 능력도 5% 확대했다.
최근에는 인공지능(AI)이 결합하면서 시너지가 나고 있다. 회사 관계자는 “설비 정비 계획을 수립할 때 AI로 고장 위험이 높은 설비를 예측하고 수학적 최적화로 정비하는 순서를 정하면 사전에 계획을 짜고 인력도 효율적으로 배치할 수 있다”고 분석했다.
강경주 기자 qurasoha@hankyung.com
관련뉴스