대구 테크노파크·섬유기계硏
공동연구로 부품 국산화 성공
전문 연구인력과 시뮬레이션
연구소 실험인프라도 큰 도움
[ 이우상 기자 ]
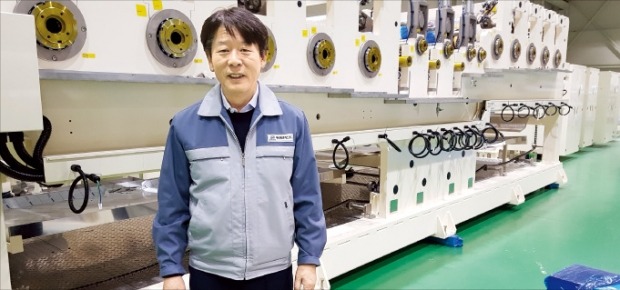
하늘에 떠 있는 별. 중소기업인들은 연구개발(R&D)에 필요한 고급인력을 이렇게 부르는 경우가 많다. 지방 중소기업이라면 어려움이 더하다. R&D에 쓸 고급인력은 별보다 구하기 어렵다는 얘기도 나온다. 대구에 있는 중소기업 명성티엔에스는 산학연기술개발사업으로 이 문제를 해결했다. 대구테크노파크에 있는 연구인력 및 섬유기계연구소의 박사급 인력과 함께 연구를 진행했다. R&D 전문인력이라곤 석사급 두 명, 학사급 일곱 명 정도밖에 없던 회사가 전량 수입하던 부품을 국산화해 제품 원가를 48% 절감했다.
국내 유일 분리막 제조 설비 턴키 공급
2001년 설립된 명성티엔에스는 2차전지에 필요한 분리막을 생산하는 설비를 만든다. 분리막은 2차전지의 양극재와 음극재 사이에 들어가는 핵심부품이다. 설립 초기에는 시장 진입에 어려움을 겪었다. 하지만 스마트폰 등 휴대용 전자기기 시장이 커지고 그 속에 들어가는 리튬 2차전지 수요가 늘자 회사도 함께 성장했다.
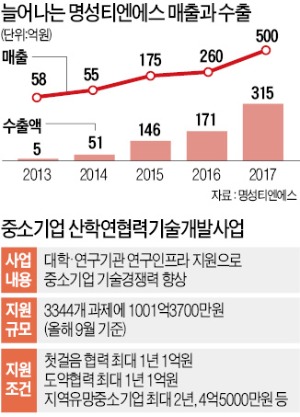
산·학·연 협력 통해 필수 부품 국산화
매출이 늘어나는 동안 명성티엔에스는 신사업도 시작했다. 분리막으로 쓸 고분자화합물 필름을 잡아당겨서 늘리는 데 쓰는 장비의 클립을 국산화하기로 결정한 것. 전량 일본에서 수입해 쓰는 부품이었다. 권 대표는 기계에 따라 적게는 몇백 개에서 많게는 2500개가 들어가는 부품이기 때문에 국산화만 할 수 있으면 생산원가를 크게 낮출 수 있을 것으로 확신했다.
하지만 쉽지 않았다. 클립이 150~200도 고온에서도 변형 없이 견뎌야 했다. 필름을 균일한 힘으로 고정하지 못하면 필름이 뒤틀려 쓸 수 없게 되기도 했다. 중소벤처기업부와 중소기업기술정보진흥원의 도움을 받은 명성티엔에스는 섬유기계연구소 연구원들과 머리를 맞댔다. 명성티엔에스가 아이디어를 내 설계해 가면 연구소의 전문연구인력이 시뮬레이션을 해줬다. 실제로 시제품을 만들지 않고도 시험해볼 수 있어 연구개발에 드는 시간과 돈이 크게 절약됐다. 세부설계도 연구소 연구원이 변경해줬다. 중소기업은 구비하기 힘든 연구소 실험 인프라도 도움이 됐다.
명성티엔에스는 지난 8월부터 산·학·연 공동으로 새로운 기술 개발에 나섰다. 분리막 필름을 단면 대신 양면으로 코팅하는 제조설비를 개발해 보기로 했다. 권 대표는 “2차전지를 사용하다 보면 발열이 발생하는데 이 열로부터 분리막을 지켜주는 것이 코팅”이라며 “양면 코팅을 하면 열에 대한 강도가 크게 높아질 것”이라고 말했다.
명성티엔에스의 매출 중 90%는 수출에서 나온다. 대부분이 중국이다.
대구=이우상 기자 idol@hankyung.com
관련뉴스