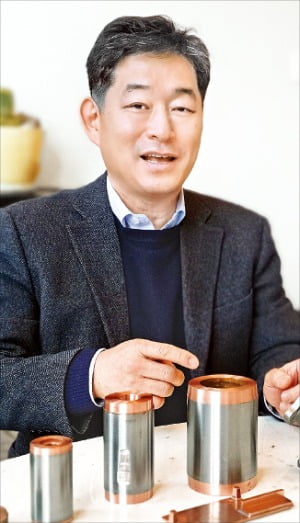
일본도 인정한 ‘구리 주조’ 기술력
구리는 다른 비철금속에 비해 끓는점이 높아 제조에 사용되는 금형의 수명이 짧은 편이다. 고열로 융해해도 급격히 산화가 진행되는 까닭에 제품의 품질을 일정하게 유지하기도 어렵다. 전 세계적으로 구리 다이캐스트 기술을 보유한 업체가 5~6곳에 그치는 이유다.
홍기원 캐스트맨 대표는 주조 엔지니어링 경력을 바탕으로 2010년 이 회사를 설립했다. 국가 전력량의 약 40%를 차지하는 유도전동기 효율화를 목표로 한국전기연구원의 연구개발(R&D) 자금 지원을 받았다. 홍 대표는 전기 전도율이 우수한 구리 회전자를 적용해야 전동기의 전기 효율을 높일 수 있다고 판단했다.
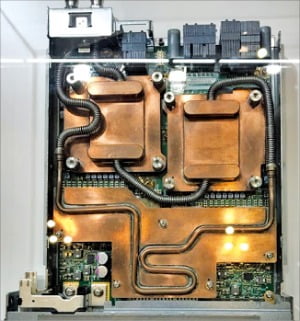
캐스트맨이 다이캐스트 방식을 적용한 구리 제품은 일반 가공 구리 제품에 비해 가격이 5분의 1 수준으로 저렴하다. 다이캐스트 제품이기 때문에 내구성과 열·전기 전도율은 주조 접합 제품에 비해 우수하다. 이 업체는 기술력을 인정받아 지난해 6월 일본 첨단 전기장비 제조 업체 후지쿠라와 구리 다이캐스트로 제조한 히트싱크(냉각용 방열기) 납품 계약을 맺었다. 일본 정부가 후지쓰에 발주한 최신형 슈퍼컴퓨터의 중앙연산처리장치(CPU) 등을 제조하는 회사다. 대량 납품이 진행되면서 이 업체의 지난해 매출은 30억원으로 전년 대비 두 배 이상 뛰었다.
솔트 코어 다이캐스트 세계 최초 상용화
캐스트맨은 다음달 다이캐스트 기술의 신기원을 열겠다고 예고했다. 세계 최초로 ‘솔트 코어’를 적용한 알루미늄 다이캐스트 양산체제를 마련해서다. 모래 대신 공업용 소금으로 제작한 솔트 코어를 금형 안에 넣어 형상을 주조하는 게 알루미늄 다이캐스트 양산의 핵심 기술이다. 다이캐스트 생산 방식을 적용하면 단위 시간당 생산량은 최대 10배까지 증가한다. 모래를 사용하지 않기 때문에 분진이 생기지 않아 환경오염도 줄일 수 있다.
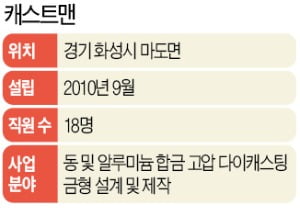
홍 대표는 “과거에 일일이 조립하던 자동차 부품을 다이캐스트 기술로 자동화를 이루게 됐다”며 “제조산업의 생산성을 수십, 수백 배 끌어올릴 기술인 만큼 베트남 등 개발도상국 업체들의 납품 문의가 잇따르고 있다”고 전했다.
캐스트맨은 자동차 터보차저 하우징, 너클 등 형태가 복잡한 정밀주조품 제조에도 솔트 코어 기술을 확대할 방침이다. 일본 최대 규모의 기계 소재 박람회 ‘M-TECH 2020’에 참가하는 등 최근 글로벌 시장 공략에도 첫발을 내디뎠다.
홍 대표는 “뿌리 산업의 침체된 분위기 속에서 핵심 분야 중 하나인 다이캐스트 전문가는 거의 없는 게 현실”이라며 “세계에 우리의 경쟁력을 입증하기 위해 애쓰겠다”고 밝혔다.
민경진 기자 min@hankyung.com
관련뉴스