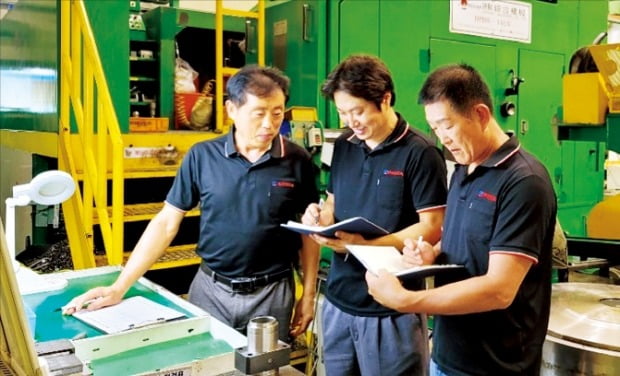
경남 김해에 있는 대정금속은 현대자동차에 자동차 엔진용 밸브와 볼트를 납품하고 있다. 이 회사는 현대차의 도움을 받아 추적이 어려웠던 불량 요인을 발견해 공정을 개선했다. 이 결과 생산량이 28% 늘고, 불량률은 61% 감소했다. 이처럼 신종 코로나바이러스 감염증(코로나19) 사태로 어려움을 겪고 있는 자동차 부품업계에서 대·중소기업 간 상생을 통한 위기 돌파 시도가 나오고 있다.
먼저 단조 시뮬레이션 시스템을 통해 볼트에 힘을 가했을 때 볼트 머리·목·몸통·나사 부분에서 응력이 어떻게 작용하는지 면밀히 점검했다. 대정금속이 생산하는 전 품목의 볼트를 대상으로 부위별로 가해진 힘의 흐름을 분석해 손상 가능성이 높은 부분을 찾아냈다. 대정금속은 이 분석을 바탕으로 5개 품목의 볼트를 새로 설계해 품질을 개선했다. 동시에 수기로 작성하던 각종 생산·품질 데이터도 전산화했다. 이 결과 재고비용을 75%나 줄였다.
현대차는 이 회사가 철근을 연결하는 커플러 제조 분야에 진출할 수 있도록 기술도 지원했다. 전기차 시대에 내연기관 부품업체들의 위기감이 커진 가운데 미래 먹거리를 찾도록 도왔다. 이 회사는 진도7까지 견딜 수 있는 ‘내진 커플러’를 개발해 수출을 앞두고 있다. 북미에서 받은 선주문 물량을 감안하면 연말까지 10만 개 이상을 수출할 것으로 예상하고 있다. 이 덕분에 매출도 전년 대비 성장세를 유지할 것으로 기대하고 있다.
삼금공업은 현대차에 도움을 요청했다. 현대차의 제안에 따라 새로운 설비를 구입하는 대신 기존 공장 내 설비를 응용해 각인 작업을 자동으로 해주는 ‘롤 마킹 자동화 시스템’을 구축했다. 이 시스템 도입으로 시간당 생산량은 1800개에서 2500개로 38%가량 증가했고, 불량률은 40% 감소했다. 이런 성과에 힘입어 올해 매출이 작년보다 8% 증가한 129억원을 거둘 전망이다.
이영수 삼금공업 사장은 “기존 제조 인력을 다른 분야에 배치해 월 평균 600만원의 인건비를 절감했다”며 “생산이 증가하면서 고용도 늘었다”고 말했다.
충남 아산의 자동차부품업체 케이디는 자동차에 들어가는 에어백 케이스를 생산하고 있다. 플라스틱 소재로 고온의 열을 거쳐 에어백 케이스 형상을 만든다. 이 과정에서 외부 기온에 따라 100분의 1㎜씩 크기에 차이가 나곤 했다. 현대차의 도움으로 수작업에 의지하던 오차 검사를 전산화했다. 이 결과 케이디는 품질을 30% 개선하면서 연간 5700만원의 비용을 절약할 수 있게 됐다고 밝혔다.
안대규/민경진 기자 powerzanic@hankyung.com
관련뉴스