본사가 있는 대만 신추에 차세대 공장을 건설 중인 TSMC가 미국에 대규모 생산 시설을 또 짓는 이유는 글로벌 공급망관리(SCM)의 재정비 때문이다. TSMC가 애플, AMD 등 미국 고객사와 더 가까워지기 위해 결단을 내린 것이다.
TSMC의 애리조나공장 신설은 코로나19 이후 글로벌 SCM 전략이 어떻게 변하고 있는지 상징적으로 보여준다. 글로벌 기업들은 최근 탈(脫)중국, 선진국으로의 생산시설 분산, 제조공정 모듈화 등을 통한 SCM 조정에 속도를 내고 있다.
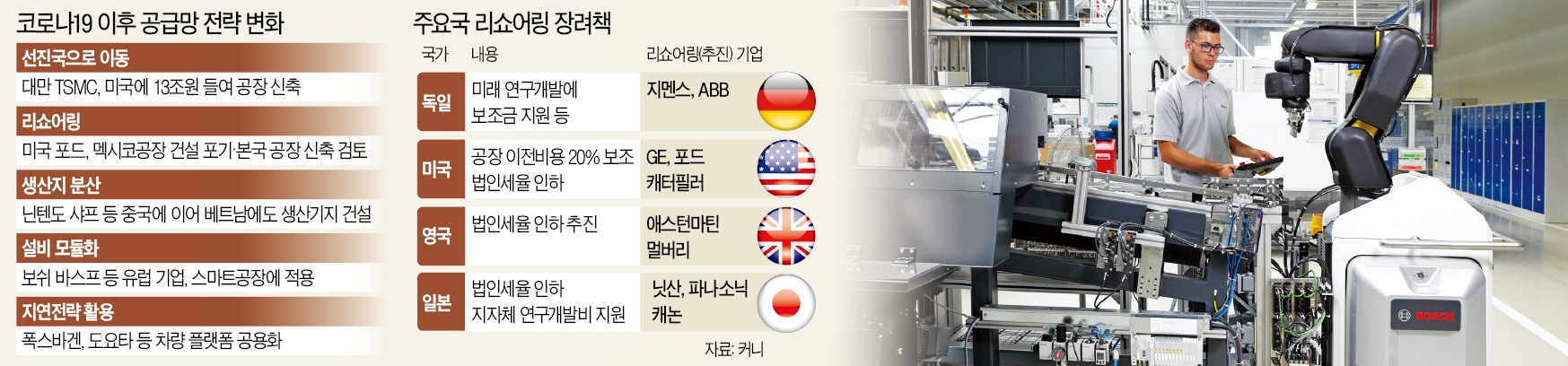
이에 따라 비싼 인건비 등을 감수하고 본국에 공장을 짓거나 대형 고객이 몰려 있는 미국 등으로 생산시설을 옮기는 사례가 늘고 있다. 미국 반도체기업의 행보가 적극적이다. 글로벌파운드리는 지난 6월 뉴욕주 몰타에 26만7000㎡ 규모 부지를 매입했다. 최신 생산시설을 짓기 위해서다. 이 회사는 “3000명을 추가 고용할 수 있을 것”이라고 강조했다. 커니 관계자는 “저비용 국가 중심의 생산 이점이 줄어들고, 판매를 위해 고비용 국가에 생산거점을 두려는 추세가 지속될 것”으로 전망했다.
생산지 조정에 따른 비용 증가는 해결해야 할 과제다. 글로벌 기업들은 설비 모듈화로 비용 증가를 상쇄하는 데 주력하고 있다. 공장 설비를 제품에 따라 레고블록처럼 쉽게 붙였다 떼었다 할 수 있도록 만드는 것이다. 설비 모듈화는 보쉬, 지멘스, 훼스토 같은 독일 기업에서 시작돼 글로벌 기업으로 확대되고 있다. 보쉬 관계자는 “생산공장은 똑똑할 뿐만 아니라 유연성도 필수적으로 갖춰야 한다”고 설명했다.
파트너사와의 협업 강화도 최근 SCM의 주요 트렌드로 꼽힌다. 공정을 분업화해야 제품 경쟁력을 높이고, 비용을 절감할 수 있다. 스마트폰 사업에서 중국 업체의 제조업자개발생산(ODM)을 확대하고, 파운드리사업과 관련된 협력사를 늘리고 있는 삼성전자가 대표적인 사례로 꼽힌다. 삼성전자는 최근 세계 2위 반도체 후공정업체 앰코 등을 파운드리 협력사로 추가했다.
사물인터넷(IoT)을 통한 스마트공장 구축도 기업들이 관심을 두는 주요 과제다. 보쉬는 IoT를 활용해 스마트공장 내 물품 이동 시스템을 구축하고, 물품에 대한 정밀한 위치 측정 등이 가능한 솔루션을 선보였다.
코로나19 여파로 SCM 전략이 바뀌더라도 본사와 각 지역에서 생산하는 제품의 품질은 균일하게 유지돼야 한다. TSMC는 대만 이외 지역에 공장을 지을 때 물류 전략, 설비 설치, 핵심 기술 등을 정리한 데이터클라우드를 활용하고 있다. 인텔 역시 글로벌 공장의 생산성 및 품질의 상향 평준화를 위해 미국 공장의 생산체계, 인적 자원, 시스템, 운영체계 등을 완벽하게 복제해 각 지역의 새로운 공장에 적용하고 있다.
황정수 기자 hjs@hankyung.com
관련뉴스