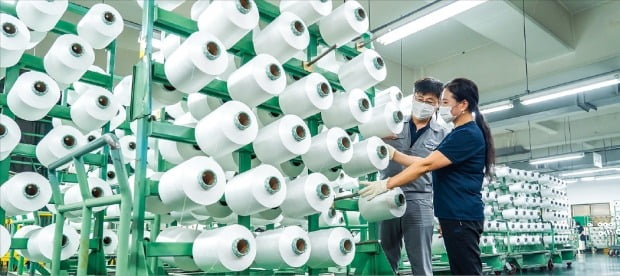
8일 경북 구미에 있는 효성티앤씨 섬유공장. 갓 뽑힌 섬유로 짠 원단의 탄성 실험이 한창 진행되고 있었다. 공장 직원들은 한 가닥씩 섬유를 풀어보며 파손된 부분은 없는지 일일이 눈으로 확인했다. 불순물을 걸러내는 작업도 이어졌다. 품질 검사 결과 문제가 없는 섬유는 쉴 새 없이 롤에 감겨 포장됐다.
이 섬유는 세계 시장 점유율 1위(33%)인 효성티앤씨의 대표 효자품목인 스판덱스. 맞은편 공장에선 폐페트병을 잘게 부숴 만든 쌀 모양의 ‘칩’을 기계에 투입하자 노즐에서 분당 4.5㎞의 하얀 섬유가 빠른 속도로 뿜어져 나왔다. 버려지는 폐페트병을 활용해 만든 친환경 섬유였다.
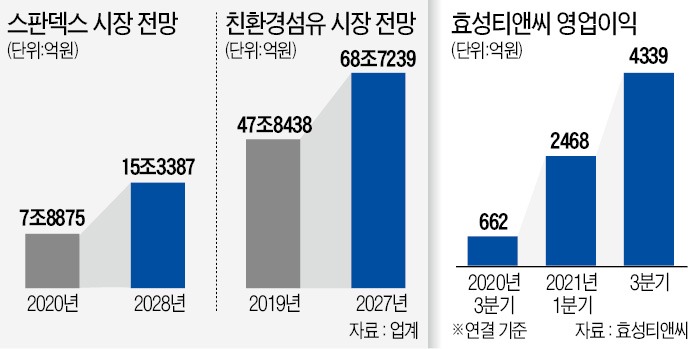
1970년대 경제성장을 이끌던 섬유산업이 친환경 첨단기술을 만나 화려하게 부활하고 있다. 섬유산업은 과거 값싼 노동력을 앞세운 대표적인 노동집약적 산업이었다. 하지만 1990년대 들어 값싼 중국산 제품에 밀리면서 입지가 줄어들기 시작했다. 정부 차원에서 중화학공업을 적극 육성하면서 섬유산업은 ‘한물간’ 사양산업으로 불리기도 했다.
그럼에도 국내 섬유기업은 사업을 포기하지 않았다. 외환위기와 글로벌 금융위기 등 잇단 악재에도 연구개발(R&D) 투자를 중단하지 않았다. 그 결과 세계 시장을 주름잡는 고부가가치·고기능성 제품을 앞세워 차세대 성장산업으로 도약하는 데 성공했다는 분석이 나온다.
효성티앤씨가 생산하는 스판덱스가 대표적이다. 고기능성 제품인 스판덱스는 BDO(부탄다이올) 등 여러 원료를 혼합해 만든 소재다. 신축성이 좋아 활동하기 편하고 건조성과 내구성이 우수해 레깅스, 등산복 소재로 활용된다. 스판덱스는 잘 늘어나면서도 끊기지 않아야 한다. 염색도 잘 돼야 하고, 고온에도 견뎌야 해 기술 진입장벽이 높은 섬유로 꼽힌다.
효성 구미공장은 연 2만4000t의 스판덱스를 생산하고 있다. 효성 스판덱스 공장 한쪽에선 연구원들이 섬유의 양 끝을 기계로 집은 뒤 끊어지기 직전까지 잡아당기는 탄성 실험을 하고 있었다. 하얀 원단이 조금씩 직조될 때마다 공장 직원들은 원단을 만져보며 구석구석을 살폈다. 구미공장의 원사 합격률은 99.9%에 달한다. 회사 관계자는 “1989년 연구개발을 시작한 이후 30년간 끊임없이 품질 혁신활동을 펼쳐 스판덱스 세계 시장 1위를 차지할 수 있었다”고 설명했다.
폐페트병을 재활용해 만든 친환경 섬유도 대표적인 고부가가치 제품 중 하나다. 효성티앤씨는 버려진 생수 페트병을 모아 세척한 뒤 칩을 만들고 250~280도 온도에서 녹여 섬유를 뽑아낸다. 월평균 300만 개 이상의 500mL 생수병이 구미공장에서 재활용되고 있다. 친환경 섬유는 일반 원사보다 1.5배 정도 가격이 비싸지만 탄소 배출량이 적어 노스페이스 등 글로벌 패션업계로부터 러브콜을 받고 있다.
갓 뽑혀 나온 섬유가 실온에서 건조되려면 용매가 증발해야 한다. 이 때문에 공장 내부는 시큼한 용매 냄새로 가득 차 있었다. 노즐에 손전등을 비추니 네다섯 갈래 섬유가 일정한 속도로 뽑혀 나오고 있었다. 공장 관계자는 “기계적 재활용으로 만드는 친환경 섬유는 굵기가 굵은 편이어서 노즐에서 뽑혀 나오는 모습을 육안으로 확인할 수 있다”고 말했다.
기계적 재활용이란 플라스틱을 기계로 분쇄해 재활용하는 방식을 뜻한다. 효성티앤씨는 기계적 재활용을 넘어 화학적 재활용을 통한 친환경 섬유 개발도 진행 중이다. 한규형 효성티앤씨 기술팀장은 “섬유는 얇을수록 부드러워지기 때문에 기술 개발에 성공하면 아웃도어뿐 아니라 이너웨어도 생산할 수 있을 것”이라고 말했다.
구미=남정민 기자 peux@hankyung.com
관련뉴스