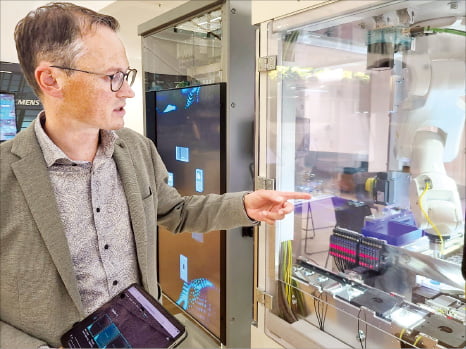
컨베이어 벨트에 달라붙어 작업하는 ‘전형적’인 제조업 근로자의 모습은 더는 찾아볼 수 없었다. 가상공간을 보여주는 모니터가 모든 행위를 대체했다. 지난 7일 독일 지멘스 암베르크공장 내부로 들어서자 가장 먼저 눈에 띈 건 생산라인에서 파란 유니폼을 입고 근무하는 직원들의 모습이었다. 구역별로 설치된 설비에서 각종 부품이 컨베이어 벨트를 통해 쉴 새 없이 쏟아져나왔지만 직원들은 컴퓨터 모니터만 들여다볼 뿐이었다. 시시각각 이동하는 부품에 일절 손을 대지 않았다. 기자가 모니터를 가까이서 들여다보니 실제 설비와 똑같이 구현된 3차원(3D) 가상설비에서 부품이 이동하는 모습을 볼 수 있었다. 지멘스가 20여 년간 수십억달러를 들여 완성한 ‘디지털 트윈’이었다.
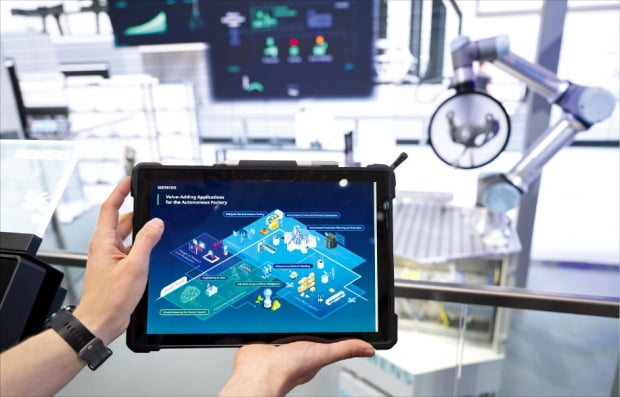
이런 간극은 생산 방식의 차이에서 비롯됐다는 것이 전문가들의 지적이다. 획일화되고 정형화된 틀에서 자동화를 통해 특정 품종을 대량생산하는 국내 기업들과 달리 암베르크 공장은 ‘다품종 대량생산’이 특징이다. 이곳에서 생산하는 주력 제품은 PLC(프로그램 로직 제어기) 제품군이다. 각종 설비 및 생산라인을 제어하는 컨트롤러로, 공장 자동화를 위한 ‘두뇌’ 역할을 한다. 지멘스는 세계 6만 개 기업에 암베르크공장에서 생산한 제품을 공급하고 있다. 공장마다 생산라인 최적화를 위한 조건이 다르기 때문에 공급해야 하는 PLC 규격도 천차만별이다. 이곳에서 생산되는 PLC 제품군은 1700종이 넘는다.
1990년대 초반만 하더라도 이곳에서 생산되는 제품군은 80종에 불과했다. 같은 기간 제품군이 10배 이상 늘었음에도 생산량은 15배 증가했다는 것이 회사 측 설명이다. 고객 주문을 받으면 부품 입고부터 제품 출하까지 24시간 내에 이뤄진다. 마르쿠스 지게르트 지멘스DI 자동화사업부 이사는 “고객이 원하는 다양한 규격의 제품을 적시에 대량 공급할 수 있는 것이 가장 큰 특징”이라고 설명했다.
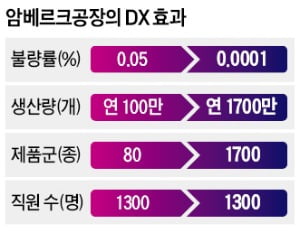
우선 컴퓨터에 구현한 가상설비에서 제품을 미리 가상으로 만든다. 수만 번에 걸친 시뮬레이션을 통해 최적의 설계 방법을 찾는 것이다. 컴퓨터가 도출한 최적의 설계안을 바탕으로 부품은 실제 생산라인에 투입된다. 이 과정에서 각종 부품엔 수천 개의 센서와 스캐너가 설치돼 어느 지점에서 어떤 부품이 잘못됐는지 실시간 확인이 가능하다.
마지막으로 제품을 생산하는 공정 단계에선 효율 개선을 위한 작업이 이뤄진다. 이른바 ‘노는’ 설비나 병목현상이 생기지 않도록 한다. 지게르트 이사는 “과거엔 제품 설계와 제조 과정의 데이터가 분리돼 있었다”며 “디지털 트윈을 통해 정보기술(IT)과 운영기술(OT)을 결합하면 설계부터 생산에 이르는 모든 과정을 시뮬레이션할 수 있다”고 말했다.
디지털 트윈은 불량률을 획기적으로 개선하는 데 성공했다. 이 공장의 불량률은 0.0001%에 불과하다. 제품 100만 개 중 불량품이 10개꼴이다. 100만 개당 500개에 달했던 1990년대 초반 대비 50분의 1로 감소한 것이다.
지멘스는 지난해 암베르크공장 바로 옆에 세계 각국에서 찾아오는 기업인과 관료들을 위한 방문자센터를 열었다. 이곳에선 지멘스가 개발한 소프트웨어(SW) 기술을 적극 알리고 있다. 안드레아 프리드리히 지멘스DI 홍보실장은 “지멘스의 디지털 트윈을 가능하게 한 원동력은 인공지능(AI), 빅데이터, 사물인터넷(IoT), 클라우드 등 SW 기술”이라고 설명했다. 지멘스는 최근 10년간 SW 관련 기업 인수에만 100억유로 이상을 투자했다. 가상 세계에서 실제 세계를 똑같이 구현할 수 있는 것도 매일 5000만 건씩 쌓이는 데이터를 앞세운 SW 분석 역량에서 비롯됐다는 게 회사 측 설명이다.
암베르크=강경민 기자 kkm1026@hankyung.com
관련뉴스