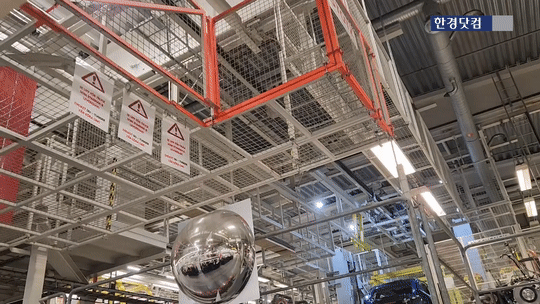
지난 5일(현지시간) 스웨덴 예테보리에 위치한 볼보자동차의 토슬란다(Torslanda) 공장. 투어 차량을 쭉 타고 공장 안으로 들어가니 트레일러를 따라 실려 오는 차량 하부구조가 보였다. 이어 그에 걸맞은 차체가 이동해 하부구조와 맞춰지는 모습을 한 눈에 볼 수 있었다. 이런 식으로 채 1분도 안 지나 또 다른 차체가 완성됐다.
이 작업은 볼보가 토슬란다 생산의 조립 공정에 새롭게 도입한 '메리지 포인트'다. 전동화 전환 계획에 따라 토슬란다 공장에 도입한 새로운 작업 방식. 복잡한 기존 방식의 작업을 단순화해 비용과 시간을 줄인다는 점이 핵심이다.
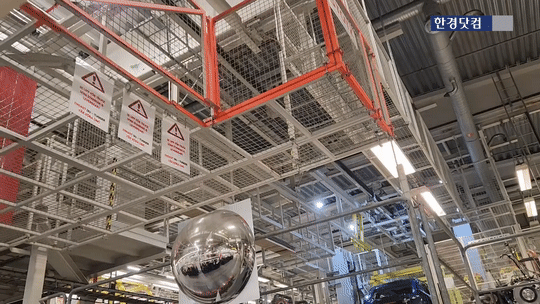
토슬란다 공장은 1964년 4월 설립된 볼보의 가장 오래된 생산기지다. 45만㎡(약 13만6000평) 규모 공장에서는 직원 약 6500명이 작업하고 있으며 연간 30만대의 볼보 차가 생산된다. 58년의 역사를 지닌 유서 깊은 토슬란다 공장도 이제는 전기차 시대에 걸맞게 변화하고 있다.
2030년 '전 라인업 전동화'를 선언한 볼보는 차세대 순수 전기차 생산 경쟁력 강화를 위해 토슬란다 공장에 100억 크로나(약 1조2647억원)을 투자, 새로운 제조 공정인 '메가 캐스팅'을 도입했다. 부품을 얻기 위해 거쳐야 했던 여러 작업 과정을 한 번에 찍어낸다. 차체 제작이나 도장, 배터리 및 차체 조립 등 생산 과정 전반의 제조 공정을 단순화해 비용을 절감할 수 있다.
공장 투어를 하면서 눈에 띈 메리지 포인트 또한 메가 캐스팅 투자의 일환으로 도입된 새로운 제작 방식이다. 볼보는 토슬란다 공장에서 전기차 생산을 위해 자동차 바닥의 형태에 따라 배터리 셀과 모듈을 통합하는 형태로 개조할 예정이다.
공장 곳곳에는 직원들을 위한 휴게실이나 라인마다 마련된 화장실, 음료수 자판기 등이 눈에 띄었다. 볼보 측은 "직원들의 쾌적한 작업 환경을 위한 휴식 공간과 라커룸 정비 등도 메가 캐스팅 투자에 포함된다"고 귀띔했다.
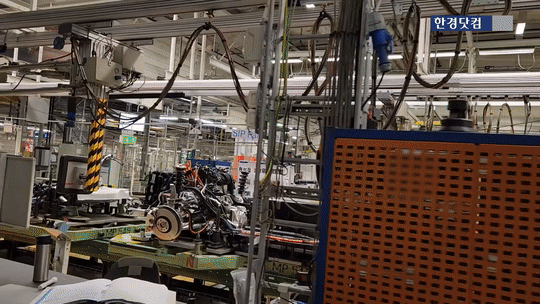
이곳에서는 1400여대의 로봇이 투입돼 용접부터 부품 조립까지 척척 해내고 있다. 투어 가이드는 한 차량당 5000번의 용접이 필요하다고 설명했다. 오렌지색, 하얀색 등 색깔마다 다른 로봇과 기계가 각각 작업하는 차종을 설명해줬다. 엔진이나 주요 부품을 결합하고 의자 등을 조립하는 일도 로봇이 한다.
대부분의 공정이 로봇을 통해 자동화됐지만, 사람이 라인에 서서 작업하는 모습도 볼 수 있다. 조립이나 차량의 이상 유무를 확인하는 품질 점검 등 꼼꼼함이 요구되는 작업에는 여지없이 사람의 손길이 닿았다. 성별 차이 없이 가능한 작업으로 투어 가이드의 설명에 따르면 토슬란다 공장의 여성 근로자 비율은 약 32%에 달한다.
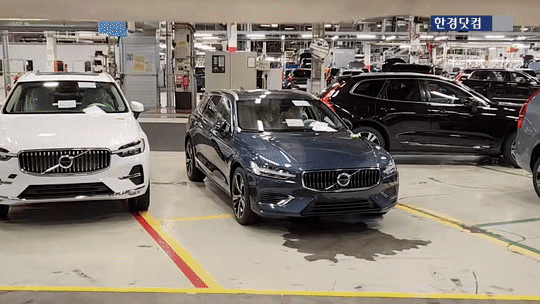
토슬란다 공장은 2008년부터 기후중립 전기로 운영됐고, 기후중립 난방 시설까지 갖췄다. 현재 난방 에너지의 50%는 바이오가스로, 나머지 50%는 주로 산업 폐열을 활용한 지역난방을 통해 공급된다.
토슬란다 공장은 2025년까지 제조 네트워크에서 생산되는 차량 한 대당 에너지 사용량을 30%까지 감축한다는 볼보의 목표에 따라 에너지 사용 저감 노력도 쏟고 있다. 2020년에는 스웨덴 가정 약 450가구 이상의 연간 에너지 사용량에 해당하는 7000MWh를 절약하기도 했다. 볼보 측은 현재 계획 중인 조명 및 난방 시스템의 효율성 개선을 통해 2023년까지 연간 약 2만MWh를 추가로 줄일 수 있을 것으로 기대하고 있다.
예테보리(스웨덴)=최수진 한경닷컴 기자 naive@hankyung.com
관련뉴스