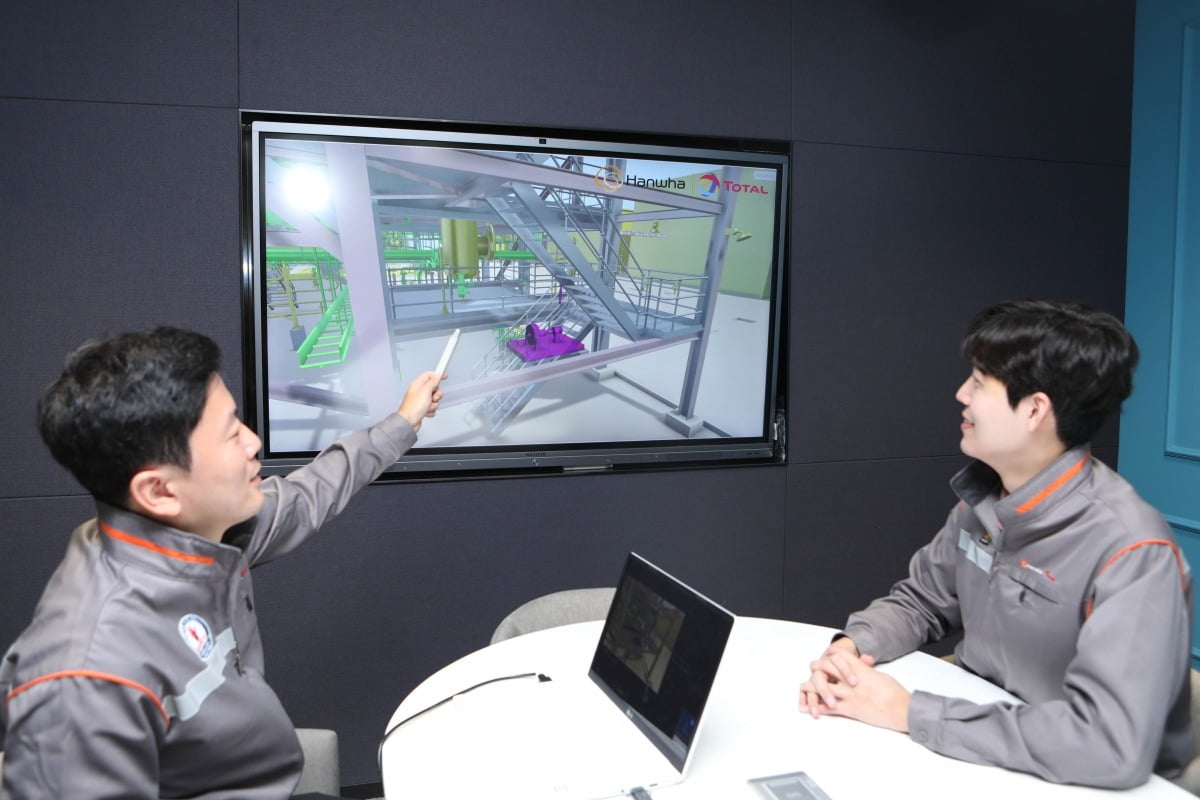
한화토탈에너지스는 ‘디지털 트윈(물리 세계를 가상 공간에 복제하는 기술)’을 중심으로 DX 혁신에 나서고 있다. 현실 세계의 공장 데이터를 가상의 공장과 연결해 시나리오별 시뮬레이션을 돌리거나 데이터 분석으로 공정·품질·설비를 개선하고 있다.
석유화학 산업의 디지털 트윈을 세 가지로 구분된다. △수급 계획, 생산, 주문, 배차, 출하, 운송, 납품 등 전 공급망을 관리하는 ‘오퍼레이션 트윈’ △공정 모니터링, 시뮬레이션 및 최적화, 자동 운전을 위한 ‘플랜트 트윈’ △설비별 데이터, 이력 관리, 정비 등을 위한 ‘에셋 트윈’ 등이다.
한화토탈에너지스는 에셋 트윈의 핵심 프로젝트인 ‘디지털 맵’에 대산 공장 전체를 복제했다. 2D와 3D 디지털 지도에 6000여 건의 중요 설비 위치를 시각화했다. 여기에 3년간 엔지니어링 데이터, 설비 보전, 검사 이력, 공장 내 작업자 데이터를 통합했다. 스마트폰 앱으로 외부 작업자 위치를 관제하는 시스템도 마련했다.
회사는 비상시 디지털 맵을 통해 전략을 수립하는 ‘비상 방제 시스템 구축’ 프로젝트도 진행 중이다. 사고 위치 근처에 있는 화학물질·설비 정보, 소방·방재 시설물 위치 등을 빠르게 파악해 대응 전략을 수립할 수 있다. 향후엔 지하 파이프라인, 고압 케이블 정보도 표시해 디지털 맵을 고도화할 계획이다.
한화토탈에너지스는 메타버스 플랫폼인 ‘게더타운’에 가상 면접장을 구축해 면접 전형에서도 DX 기술을 접목했다. 게더타운에 접속한 구직자가 면접 대기 중 회사에 대한 정보를 다양한 콘텐츠로 접할 수 있도록 마련했다. 이 회사가 가상 면접장을 구축한 것은 사내 가상 오피스가 업무 효율성을 높이는 데 도움이 됐다는 판단에서다.
한화토탈에너지스는 2017년 국내 석유화학기업 최초로 단지 내 무선통신망(P-LTE망)을 구축하기도 했다. 이를 통해 사람이 진입하기 어려운 고온·고압 환경 속 데이터를 수집할 수 있는 인프라를 마련했다. 공장 내 수집된 데이터는 품질 개선, 생산 효율성 제고에 이용된다. 공장 내 700여 대 CCTV로 촬영한 영상도 안전 가동을 위해 쓰이고 있다.
한화토탈에너지스는 DX 기술을 개선해 공장운영과 생산 효율성을 극대화하는 ‘스마트 플랜트’로 도약하겠다는 방침이다. 회사 관계자는 “전통 장치 산업인 석유화학과 4차 산업혁명을 결부시켜 데이터로 의사를 결정하는 ‘지능형 공장’으로 탈바꿈하는 것이 최종 목표”라고 말했다.
김형규 기자 khk@hankyung.com
관련뉴스