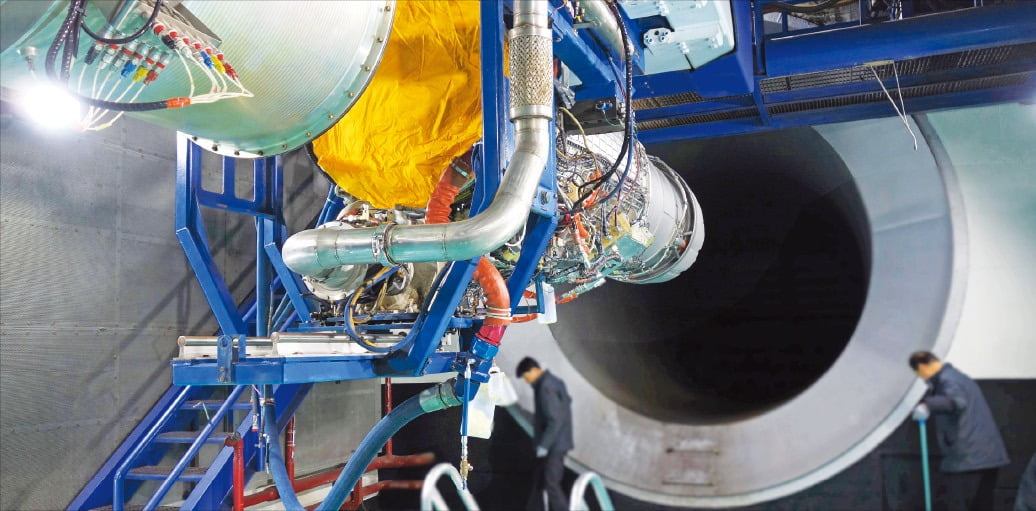
한화그룹이 전투기, 군함, 전차, 자주포 등의 동력원으로 쓰이는 ‘가스터빈 엔진’을 방위산업 분야 미래 성장동력으로 정했다. 연내 경남 창원공장의 가스터빈 엔진 생산 규모를 두 배 늘리는 동시에 2040년까지 자체 설계 기술도 확보해 설계부터 제조까지 100% 국산화한다는 목표를 세웠다. 가스터빈 엔진은 워낙 많은 군장비에 활용돼 ‘방위산업의 심장’ 또는 ‘방위산업의 반도체’로 불린다.
압축된 공기를 연료와 함께 폭발시킬 때 나오는 에너지를 동력으로 삼는 가스터빈 엔진은 성능 면에서 디젤 엔진보다 한 수 위다. 더 빠르고 힘도 세다. 한화가 자체 설계 기술을 확보해 100% 국산화하려는 건 이 중에서도 전투기용이다. 전투기에 들어가는 가스터빈 엔진은 높은 고도와 빠른 속도, 고온을 버텨내야 하기 때문에 기술 난도가 가장 높다.
한화는 자체 설계기술 없이 면허생산 방식으로 전투기용 가스터빈 엔진을 제작하고 있다. 45년째 한우물을 판 덕분에 최근 미국 제너럴일렉트릭(GE)이 “다른 나라에 있는 GE 협력업체에 제조기술을 가르쳐줄 수 있느냐”고 부탁할 정도가 됐다. GE는 미국에 있던 일부 생산라인을 2004년 아예 창원공장으로 옮겨 부품 생산을 맡기고 있다.
이 회사의 가스터빈 엔진 누적 생산량은 4월 1만 대를 돌파한다. 한국 방산 역사에서 기념비적인 일이라는 게 회사 측 설명이다.
김 상무는 “지금 생산하는 엔진은 GE, 롤스로이스, 미국 프랫앤드휘트니(P&W) 등으로부터 라이선스를 받아 조립하는 형태”라며 “60종 이상의 소재를 순차적으로 개발해 현재 39%인 가스터빈 엔진의 국산화율을 단계적으로 끌어올릴 계획”이라고 말했다.
가스터빈 엔진 국산화 프로젝트는 15년가량 걸리는 장기 프로젝트다. 워낙 변수가 많아 성공 여부도 보장하기 힘든 분야다. 하지만 재래식 무기 제조가 중심인 한국 방산업이 첨단 무기 생산으로 한 단계 올라서기 위해선 자체 설계 기술 확보는 필수라고 한화는 판단했다.
김 상무는 “4세대 전투기까지는 면허생산 및 정비가 가능했지만 F-35 등 5세대 이후 전투기부터는 불가능하다”며 “첨단 가스터빈 엔진이 들어가는 5세대 이후 전투기, 순항 미사일, 차세대 군함 등을 건조하려면 자체 설계 기술이 꼭 필요하다”고 말했다.
가스터빈 엔진 국산화는 김동관 한화그룹 부회장의 역점 사업이다. 김 부회장은 최근 창원공장을 찾아 “항공 엔진 국산화 프로젝트는 사업논리를 떠나 (국가 안보 등을 위해) 후대에 물려줘야 할 의미 있는 일”이라고 말했다.
창원=김형규 기자 khk@hankyung.com
관련뉴스