원형 셀에서 작업자 1명과 로봇의 협업…'고객맞춤형 소량생산' 방식
'AI와 로보틱스 결합' HMGICS 공개…車조립 자동화율 46% '세계 최고'
옥상엔 620m 길이 주행시험장…1층엔 스마트팜도
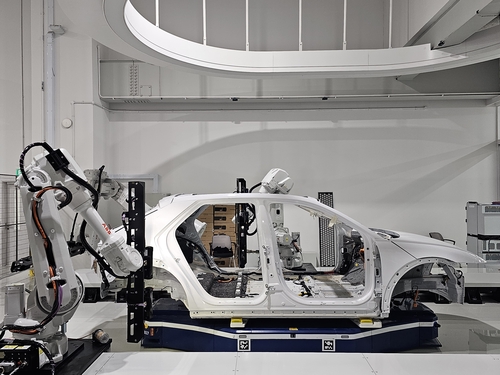
(싱가포르=연합뉴스) 임성호 기자 = 자동차 공장인데 어디에도 컨베이어벨트가 보이지 않았다. 대신 타원형 형광등처럼 생긴 흰색 조립대만 곳곳에 있었다. 그 아래에서는 단 한 명의 작업자가 현대자동차의 전기차 아이오닉5 차체에 부품을 조립하고 있었다.
부품은 바퀴 달린 로봇이 날라다 줬고, 조립이 끝나자 로봇의 품질 검사가 시작됐다. 작업장엔 사람보다 다양한 로봇이 더 많이 눈에 띄었다.
현대차가 싱가포르 스마트 산업단지인 주롱 혁신단지에 개관한 '현대차그룹 싱가포르 글로벌 혁신센터'(HMGICS) 생산라인의 풍경이었다.
현대차는 공식 준공에 앞서 지난 16일(현지시간) 국내 언론사를 대상으로 HMGICS 시설 일부를 미리 공개했다.
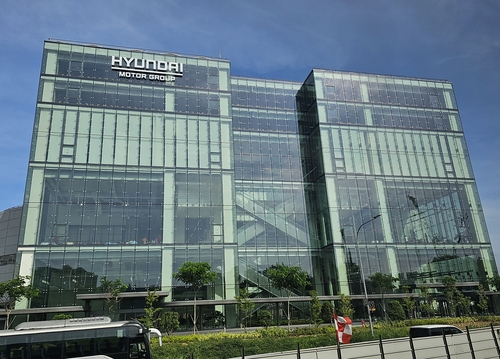
지하 2층, 지상 7층 규모 HMGICS의 3층 생산라인. HMGICS가 스마트팩토리임을 압축적으로 보여주는 공간이다.
생산라인에는 컨베이어벨트 대신 가로 약 5m, 세로 약 3m의 동그란 소규모 작업장 '셀'(cell)에 작업자 한 명과 4족 보행 로봇 한 대만 자리하고 있었다.
셀에서 양팔을 들어 부품을 조립하는 직원은 검은색 멜빵 형태의 작은 보조 기기를 등에 멘 상태였다. 작업자의 피로를 덜어주기 위해 현대차가 자체 개발한 보조 기기라고 한다.
HMGICS에는 이런 셀이 27개 설치돼 있다. 공정별로 여러 셀을 거쳐 생산하는 전기차는 연간 3만대 수준이다. 연간 수십만대를 생산하는 다른 현대차 공장에 비해선 지극히 작은 규모다.
이는 '소품종 대량생산'에서 벗어나 '고객 맞춤형 다품종 소량생산'을 위한 것이라는 게 현대차의 설명이다.
고객이 스마트폰을 통해 신차를 주문하면 즉시 HMGICS의 셀에서 맞춤 생산을 하는 방식이다. 비용 문제로 고급차에나 적용됐던 다품종 소량생산의 적용 범위가 인공지능(AI)과 로보틱스 기술에 힘입어 확대된 것이다.
셀 하나를 추가로 설치하는 데에도 사흘이면 충분하다. 주문량이 급격히 늘더라도 신속히 대응할 수 있다는 뜻이다.
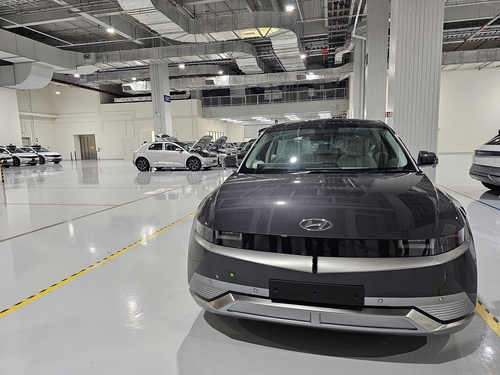
개별 공정은 물론 작업 보조와 점검까지 상당수 작업을 로봇이 담당하는 것 역시 지능형 공장 HMGICS의 특징이었다.
인간 작업자의 차체 조립이 제대로 이뤄졌는지 확인하는 일은 현대차그룹 산하 보스턴다이내믹스의 4족 보행 로봇 '스팟'의 몫이었다. 노란색 '로봇 개'처럼 생긴 스팟은 사진을 찍어 AI 시스템으로 실시간 전송한다.
이 시스템은 부품의 정상 조립 여부를 판단해 부족한 부분을 발견하면 작업자가 현장에서 수정할 수 있도록 피드백을 준다. 불량 판단의 정확도는 99% 이상으로, 인간보다 훨씬 더 정확하고 빠르게 판별할 수 있다.
셀 사이를 분주히 오가는 자율주행 운송 로봇(AMR)들은 1·2층 부품 창고에서 AI의 재고관리에 따라 공급되는 부품을 각 셀로 날라줬다.
현대위아에서 제작한 AMR에는 라이다(LiDAR) 등 센서가 달려 유도선이나 인간의 조작 없이도 사람과 장애물을 실시간으로 피했다. 사람이 빠르게 걷는 속도인 초당 최대 속도 1.8m로 움직이며 재빠르게 부품을 나르다가 배터리 용량이 20% 아래로 떨어지면 스스로 충전기로 돌아갔다.
조립이 어느 정도 이뤄진 차체 이동에는 현대로템의 무인운반차량 로봇(AGV)이 나섰다. AGV는 바닥에 부착된 QR코드를 읽으면서 나아갈 길을 찾아 셀에서 셀로 이동했다.
현지 직원 스펜서 리 씨는 "이전에 근무한 항공 제조업계에서는 자동화에 크게 투자하지 않았는데, HMGICS에서는 많은 로봇을 활용해 자동화를 한 점이 놀랍다"고 말했다.
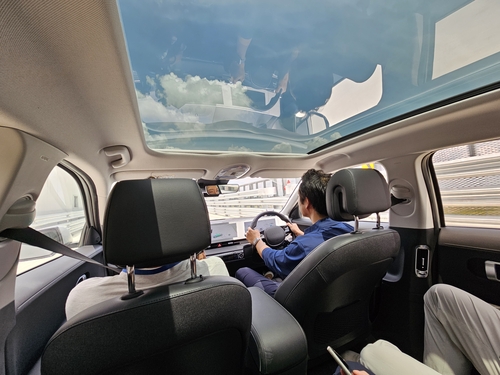
HMGICS의 연구개발 인력을 포함한 전체 직원은 280여명이다. 동시에 산업용 로봇 80여대, AMR 등 모바일 로봇 180여대가 배치돼 있다. '사람 반 로봇 반'으로 자동화율이 높아졌다.
허일권 HMGICS 생산실장은 "현재 조립 공정의 자동화율은 46% 수준인데, (일반적인) 현대차 공장은 평균 10% 정도"라고 설명했다.
3층에서 한 층을 올라가자 종합상황실 격인 '디지털 커맨드 센터'(DCC)가 있었다. 이곳에서는 물류·생산 라인의 모든 작업 상황을 대형 모니터를 통해 실시간으로 들여다보며 문제에 대응한다.
HMGICS 관계자는 "현장의 모든 부분을 데이터화해 일목요연하게 분석하고, 문제의 원인을 찾아 각 담당자가 협의할 수 있도록 돕는 것"이라며 "디지털 트윈으로 현장과 동일한 3D 공간을 구축해 실제 라인에 가서 확인하지 않더라도 좀 더 빠르게 조치가 가능하게 했다"고 말했다.
DCC는 향후 작업자와 로봇의 움직임도 디지털화해 공장 운영을 최적화할 계획이다.
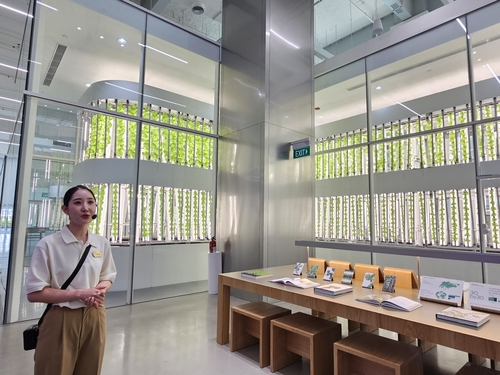
HMGICS에서 생산된 아이오닉5는 곧바로 건물 옥상 격인 5층의 주행시험장 '스카이트랙'으로 옮겨진다. 약 620m 길이의 직선 코스와 최대 기울기 33.5도의 코너링 코스를 갖춘 고객들의 시승 공간이다.
HMGICS 1층에는 공장이 아닌 농장이 자리했다. 미래형 농장 '로보틱스 스마트팜'이었다.
이곳에서 5개의 로봇 팔은 상추 등의 씨앗을 심고 약 40일 뒤 수확까지 해낸다고 한다.
HMGICS 관계자는 "현대차그룹은 혁신적인 로보틱스 기술을 통해 작은 땅으로도 최대한의 수확량을 확보하고, 신선한 작물을 바로 재배해 볼 수 있는 스마트팜을 통해 싱가포르 농경의 미래 비전을 제시하고자 한다"며 "수확한 농작물은 내년 2분기 개관 예정인 HMGICS 내 식당에서 사용될 계획"이라고 말했다.
<YNAPHOTO path='AKR20231120152500003_06_i.jpg' id='AKR20231120152500003_0601' title='로보틱스 스마트 팜' caption='[촬영 임성호]'/>
sh@yna.co.kr
(끝)
<저작권자(c) 연합뉴스, 무단 전재-재배포 금지>
관련뉴스